AGV (Automated Guided Vehicles)
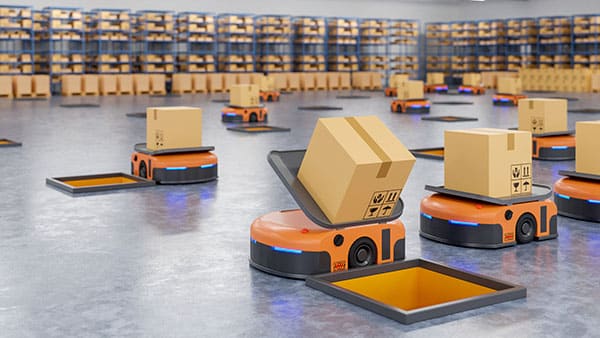
(Automated guided vehicle) AGV.3d rendering
The term AGV which stands for Automatic Guided Vehicle is generally used to identify vehicles capable of moving and doing special work independently without operator assistance. Various types of AVG are used in almost every finished goods manufacturing industry to move a wide variety of products (usually using pallets). The functions performed by AGV are similar to those of human-driven lift trucks.
Over the past few decades the shift to automation systems without operators has been seen in most manufacturing industries where they complement processing and packaging lines with automation systems that reduce the role (and number) of operators simply by supervising and controlling. This trend has also spread to internal logistics. The upstream parts of the production process are now handled automatically by a system that manages finished products, pallets and raw materials, which runs under the control of software that is able to continuously monitor operating parameters and determine the tasks and roles of each unit .
Companies from various industrial sectors of finished products are increasingly required to implement this system. One of the demands for the application of this system is the safety factor where lift-trucks that are controlled by operators are one of the main causes of accidents in the workplace. Work carried out by traditional lift-trucks is susceptible to fatigue, stress, due to uncomfortable positions or work environments. Sometimes uncontrolled lift-trucks manoeuvres cause damage to the finished product.
Another driving factor is the need to reduce production costs through reducing the number of personnel at the beginning and end of the production line.
But that is not all, by automating the internal logistics system traditionally monitored by humans, it allows full tracking of the position, amount and condition of the material (traceability) so that potential losses can be eliminated. This system has been proven to be able to increase the competitiveness of many companies.
Seeing the need for AGV, our company made an AGV prototype for a Spunbond company in Krian, East Java. The AGV consists of 4 magnetic sensors that function as directors of the path that must be traversed by AGV, 4 motors as movers, and 1 PLC that functions as AGV motion controllers. AGV is used to carry the Spunbond roll to the Sliter machine. There are 6 stations that become AGV stops. The AGV will stop at the station determined by the operator.
To learn more about how we can help you with AGV (Automated Guided Vehicle) for your company, please do not hesitate to contact us.
Related Blog
- AGV (Automated Guided Vehicles)
- Rotary Clipper
- Rekomendasi Relay Omron Terlaris untuk Penggunaan Umum
- Trik Membedakan Limit Switch Omron Asli dan Palsu
- Cara Kerja Relay OMRON Beserta Spesifikasi dan Fungsinya
- Mesin untuk Industri yang Harus Dimiliki Beserta Kegunaanya
- Mengetahui Cara Kerja Circuit Breaker Lebih Jauh
- Cara Efisiensi Distribusi Listrik pada Bangunan
- Slim Relay Omron, Inovasi Panel Control yang Hemat Ruang 50%
- Omron Sysmac Studio, Software Pilihan untuk Industri Anda
- Seluk Beluk Relay OMRON My-Gs
- Tampilan Asli Produk Timer H3CR OMRON
- Mengenal Building Automation System
- Pengantar Circuit Breaker: Fungsi dan Prinsip Kerjanya
- Sensor: Penjelasan, Cara Kerja, Jenis, dan Penerapannya
- Power Supply dalam Elektronik: Pengertian, Fungsi dan Proses Kerjanya
- Mengenal Lebih Dalam: Limit Switch dan Prinsip Kerjanya
- Linear dan Rotary Actuator, Apa Saja Perbedaannya?
- Mengenal Temperature Controller dan Cara Kerjanya
- Mengenal Perbedaan Saklar dengan Relay
- Penerapan Sistem Monitoring Energi dalam Menghemat Biaya Operasional Industri
- 8 Manfaat Sistem Monitoring Energi untuk Industri
- Cara Memilih Sistem Monitoring Energi yang Tepat untuk Bisnis Anda
- 10 Alasan Sistem Monitoring Energi Penting untuk Industri Manufaktur
- Cara Kerja Sistem Monitoring Energi untuk Meningkatkan Efisiensi Energi
- Delta PLC Programming